Waterjet Cutting
Waterjet cutting is an extremely versatile fabrication method. Waterjets can cut many different materials into almost any desired shape, making them a very effective cutting instrument, especially for complex or unique parts.
What is Waterjet Cutting?
Waterjet cutting is a process that uses a highly pressurized stream of water to cut through material. Waterjets are very powerful machines that are used in a variety of industries, including aerospace, food processing, automotive, architecture, construction, HVAC, electronics, and more. They are widely used due to their versatility, efficiency, and precision.
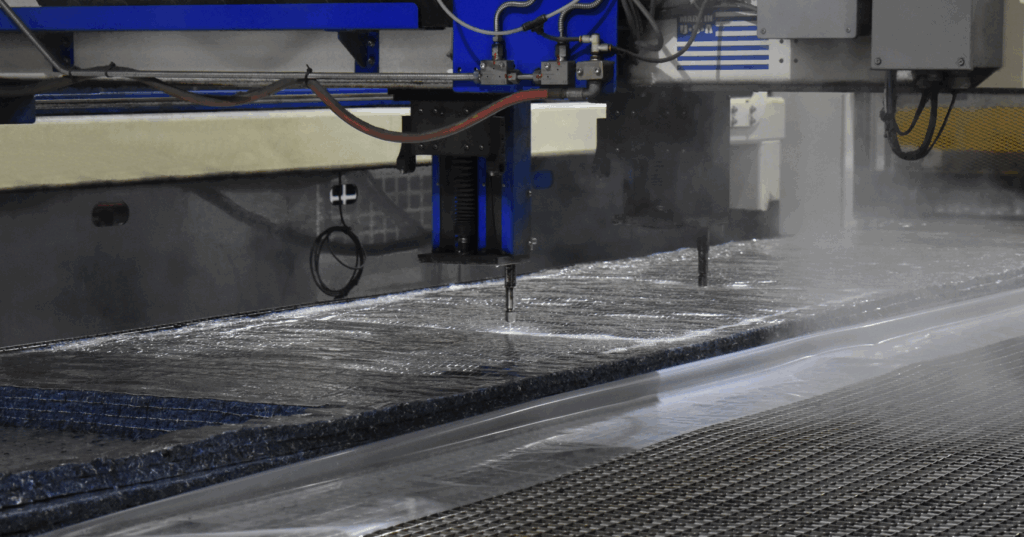
Types of Waterjets
There are two types of waterjets: Abrasive Waterjets and Pure Waterjets. Abrasive Waterjets add small abrasive particles to the water such as garnet, sand, or aluminum oxide. This extra friction increases the cutting power, allowing the waterjet to cut through dense materials like granite and steel, while still providing a clean cut.
Pure Waterjets use only highly pressurized water to cut material. This type of waterjet is used for softer materials like foam, thin plastic, fiberglass, paper board, and rubber.
How do Waterjets Work?
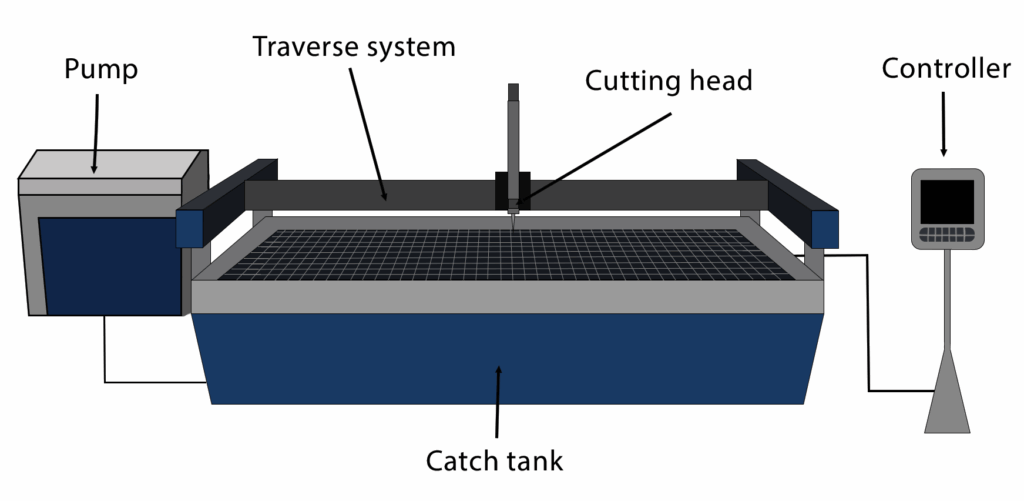
First, water is pressurized in the pump starting at 30,000 psi, and sometimes reaching pressures as high as 90,000 psi. To put this measurement in perspective, the working pressure of most fire hoses is 150-300 psi.
The pressurized water travels to the cutting head through high-pressure tubes in the traverse system. The water then passes through a hard jewel or orifice in the cutting head where the pressure creates velocity.
For an abrasive waterjet, abrasive materials are then added to the pressurized water in the cutting head. The water and abrasion material are combined in the mixing chamber.
A thin stream of water exits the cutting head at an extremely high velocity to cut the desired material in the path designated by the controller. The water stream can reach a velocity greater than 3x the speed of sound.
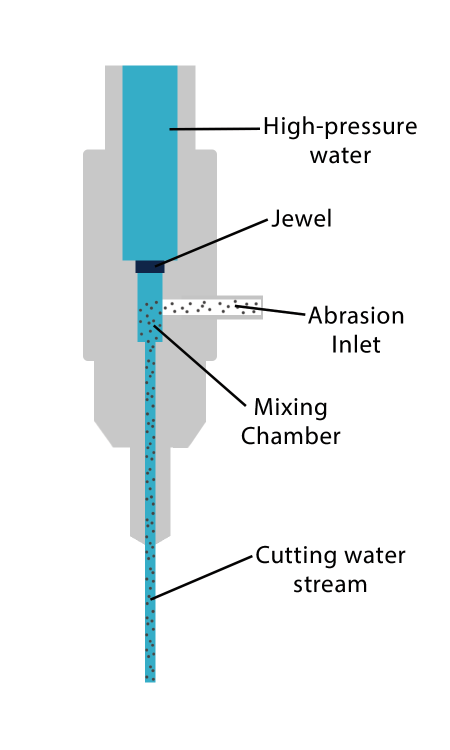
Benefits of Waterjet Cutting
High Precision
One benefit of waterjets is that they are extremely precise and can achieve tolerances tighter than +/- 0.005″. They also have the unique ability to vary tolerances for different areas of a part.
Superior Edge
Waterjets can produce parts with smooth, burr-free edges. In many cases, this eliminates the need for a secondary finishing process.
No chemicals or HAZ (heat affected zone)
Waterjet cutting is a cold cutting process. This eliminates the possibility of warping, distortion, or material stress that can occur with thermal cutting methods like laser or plasma cutting.
Safety
Waterjets are a safe option for both the operator and the environment because they do not produce toxic vapor, smoke, or dust.
Disadvantages of Waterjet Cutting
Tapering
Occasionally, a waterjet cut can result in a taper, or a difference in width throughout the cut. This is typically due to cutting too fast or slow, using a material that is too thick, or calibration and setup issues.
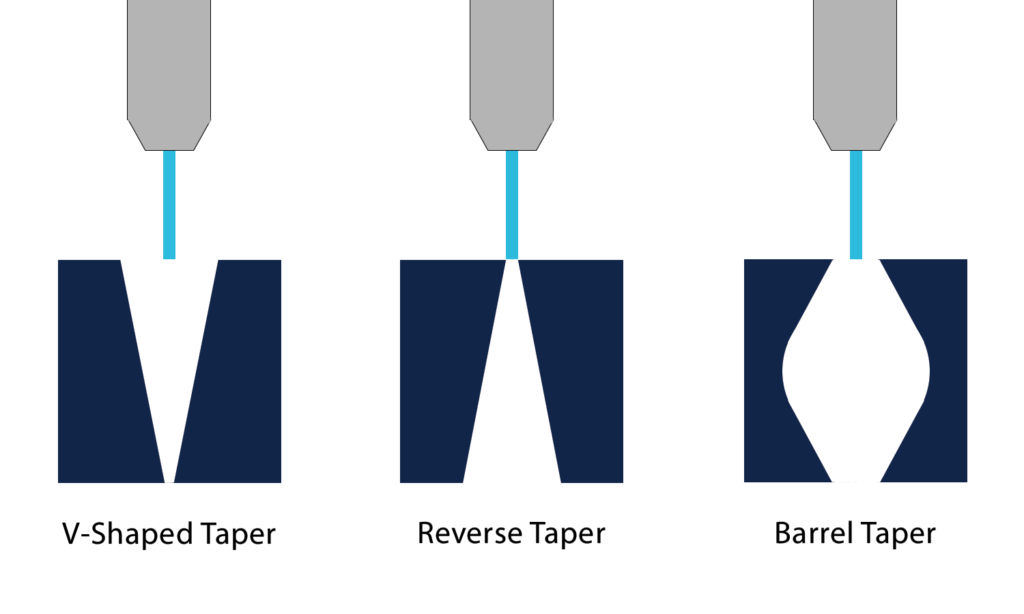
Cutting time
Waterjets typically require more time than other cutting methods. If you try to rush a waterjet, the cuts will become less accurate and precise.
Orifice failure
Low-quality waterjet orifices or jewels may break down, which would disrupt cutting and result in lost time.
When should I use Waterjet Cutting?
Because of the cutting time that waterjets require, waterjet cutting is a great option for lower volume orders and prototypes.
Waterjets are also a good option for parts that require more complex cuts. 5-Axis waterjets are perfect for more specialized parts because they offer a greater range of motion than most cutting processes. The extra range of motion can be created by adding a rotating head to a traditional waterjet or mounting the head on a robotic arm. This type of waterjet can cut in multiple directions at different angles, so it can complete a part in one process that would require multiple processes on conventional machines. This makes 5-axis waterjets a quicker, more cost-effective option for complex parts.
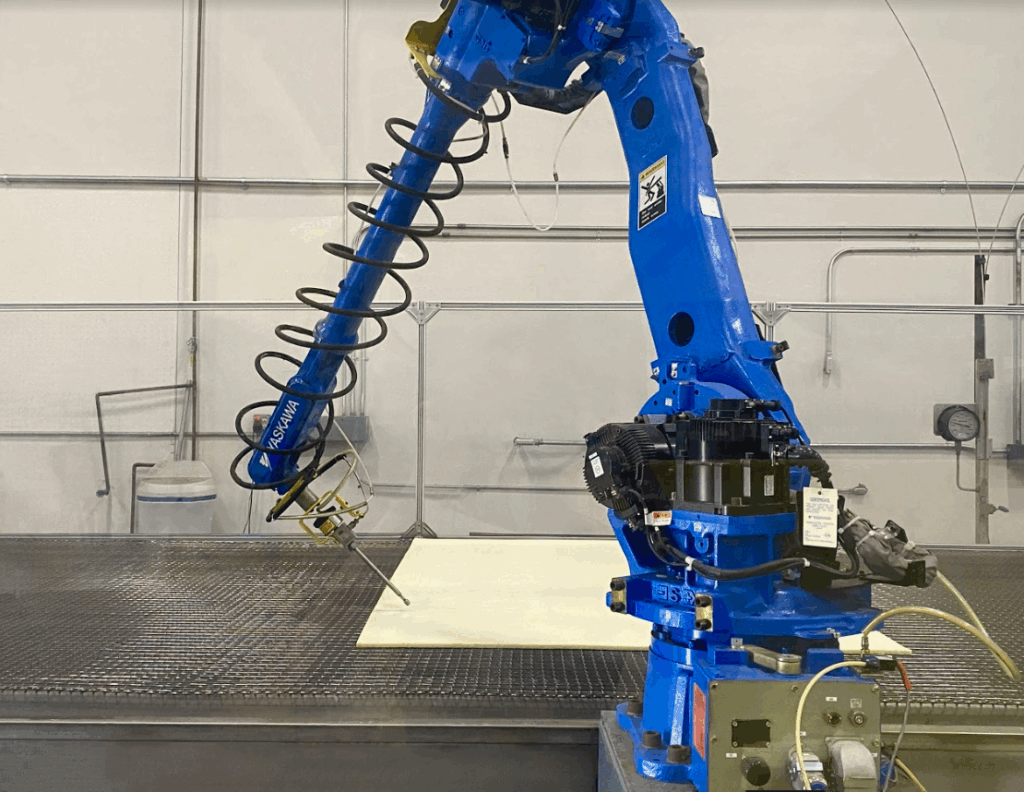
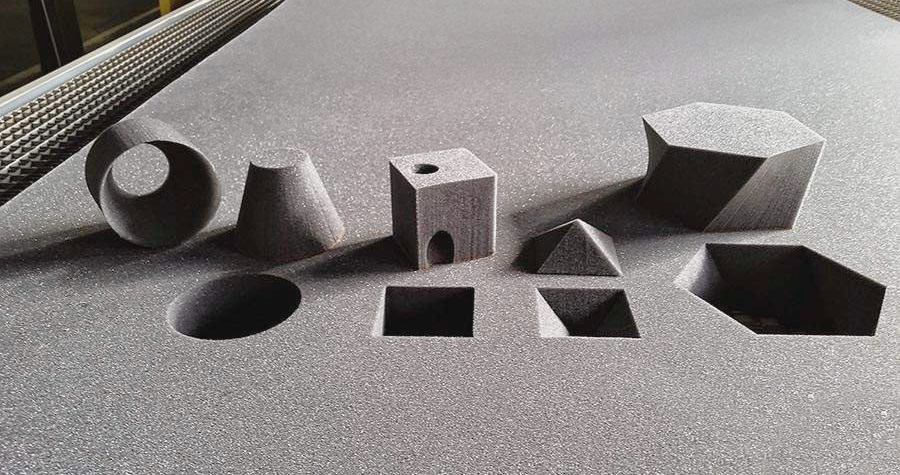
Interested in comparing waterjet cutting to other cutting processes? Check out PSC Industries’ other capabilities here!